Quality, it’s about leadership. Right?
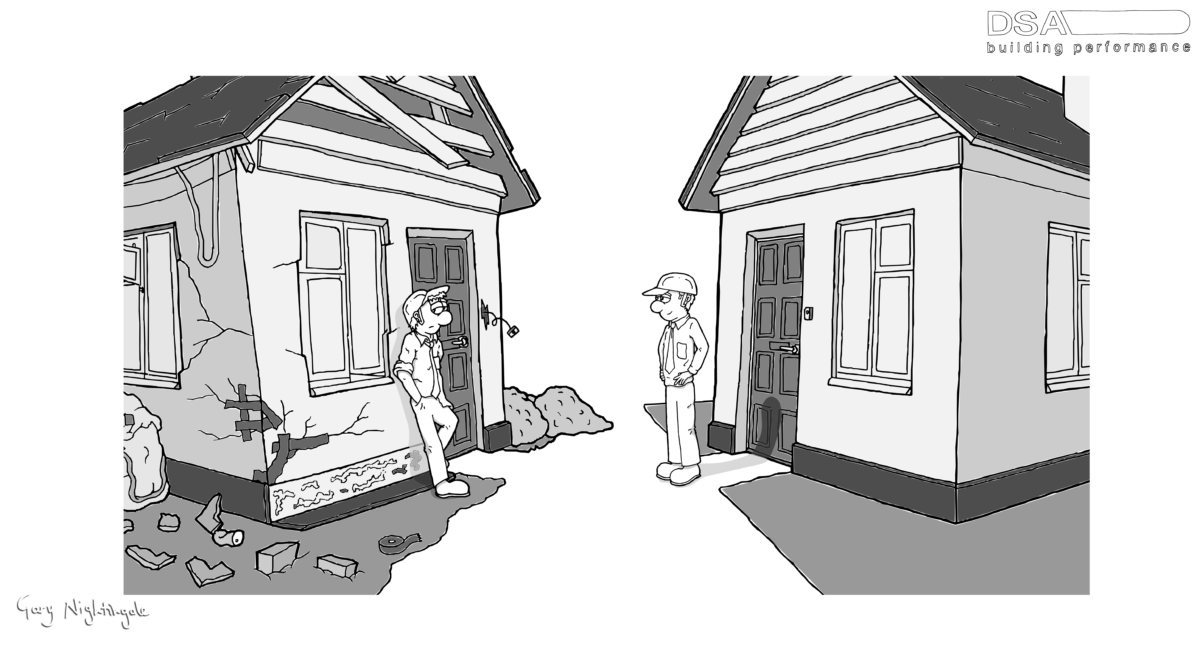
If you’re a leader in the construction industry and up for your thinking being challenged, this is for you.
By the way, you’re under no obligation to agree with anything I say.
What if I made the bold assertion that all you need to know about quality is right here, right now?
Would you pass it off as hype, or a quick fix or something that’s got nothing to do with you? If so, stop reading and move on to something more important.
Because I’m making that bold assertion.
Who cares about quality anyway?
Over the years I’ve come across few leaders who talk much about quality. Safety, yes, definitely, but quality rarely gets a mention. And that is a problem.
Show me someone who cares and I will show you quality work.
Show me quality work and behind it I will show you someone who cares.
And that is it. Quality is about people caring for the work. It’s a “people” thing, which means it’s a leadership thing. And that means you.
Leadership is about creating an environment where people care about and can do their best quality work.
If you are not actively creating that environment then you are probably a manager in a leadership role.
Engineering is about designing and sorting technical stuff.
Management is about the organisational mechanics of getting stuff done.
Leadership is about providing direction and creating the environment for success.
What best describes you?
The Four Absolutes of Quality
In his book Quality Without Tears, Philip B Crosby sets out four absolutes.
- The Definition of Quality is what the client wants and is paying for. Rolls Royce or Mini?
- The Standard is zero defects: the product is right, complete, without faults. It was Crosby who coined the term “zero defects”, not as some quality initiative but the standard set. If you set the standard at 95% you will get 70%. The standard is 100%. Setting the standard is an act of leadership.
- The Process for quality is right first time. No jack hammering out concrete, no need for retrospective checking and form filling: the work is planned and executed once.
- The Measure is the cost of quality, how much it has cost to get to what the client wants with zero defects, and anything less than that is the cost of quality.
1.2 buildings for each client and they are paying for it.
Back in the mid 90s as a contracts manager, I used to get my sites to record the Cost of Quality in a simple way: a quick estimate of the cost of reworking divided by the value of work in the month, expressed as a percentage. It came out at about 5% each month for each site. And that was just the reworking that was owned up to and recorded. Sobering when you think contractors return about 2% profit.
At that time a competitor company reckoned they built 1.2 buildings for every client, a Cost of Quality of 20%. This was a more honest assessment than I was getting though still probably the tip of the iceberg in the construction industry.
And who is paying for that? Not the contractor, they don’t have a 20% provision in their price. The client is paying for it and still is now.
People have to feel psychologically safe to own up to mistakes and rework; again, we are back to creating the right environment and leadership.
Am I bothered?
So, as a leader in the construction industry, is quality at the top of your agenda? Is it even on your agenda, or is it down to the QA manager?
Do you know what the Cost of Quality is for your organisation or department or project?
Poor quality is hitting your bottom line and your reputation with your people, supply chain and clients.
It continues to damage the reputation of the construction industry.
Show me someone who cares and I will show you a great leader and a successful organisation.